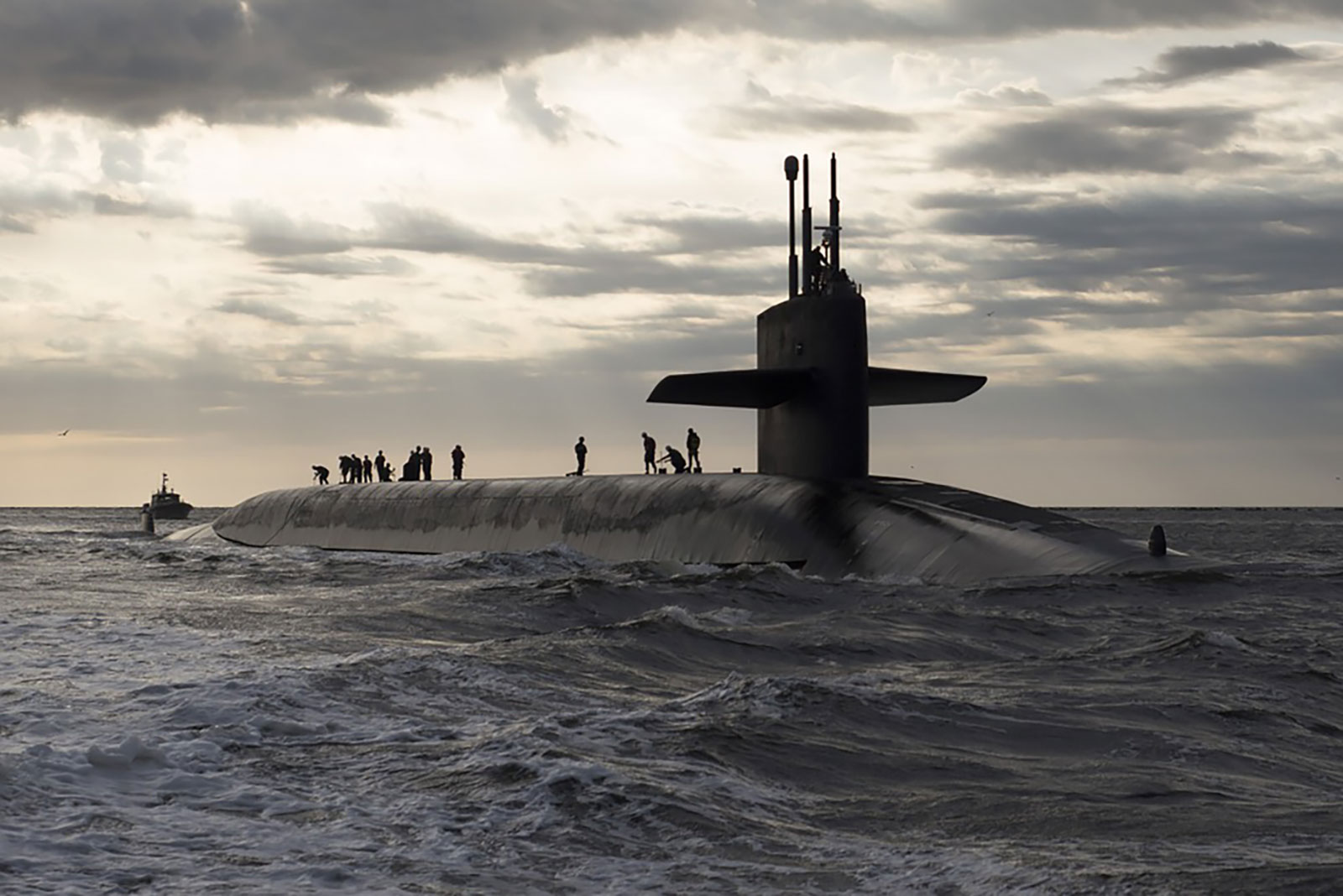
This summary is an excerpt from the Naval Engineers Journal published on 10/11/10.
By David C. Johnson, George M. Drakeley, Thomas N. Plante, William J. Dalton, & Christopher S. Trost
Achieving cost reduction in the production of complex assets – such as aircraft and satellites, ships and oil rigs, and power plants – often means making extensive change to underlying design, assembly-line processes, materials and schedules.
But large changes to production can also be a source of cost growth. This is because change – even if intended to improve efficiency or enhance capability – commonly disrupts the natural ‘learning’ through which unit production costs and schedules improve over time. This ‘learning’ is something that only occurs when productivity increases (the same tasks are accomplished with less effort) and/or rework is reduced (fewer errors are made, reducing iteration and effort needed to complete work).
To manage change in the production of complex assets, you need to use a clear understanding of the causes of disruption to find the right balance of cost reduction measures.
Identifying the causes of poor productivity
The causes of poor productivity and the need for rework in the production of complex assets are many, but must be identified early on. They can include design/planning maturity, material availability, workforce experience, prior work availability and quality, out-of-sequence working, overtime, schedule pressure and morale. While many of these causes of poor productivity tend to improve over the course of a program – design deficiencies are found and fixed on early production units, supply chain problems are worked out early on, work sequences are refined – this process can be disrupted by efforts to achieve cost reduction. Changes that lower design maturity or create new issues with material, for example, may affect these same drivers of productivity and quality adversely.
Balancing cost reduction mechanisms
Successfully balancing cost reduction mechanisms during complex programs – ie implementing changes while maintaining natural ‘learning’ in serial production – requires skill and experience, and/or analytic insight. By representing cause-effect relationships driving productivity and rework, you can use dynamic program simulation to predict likely performance under baseline and ‘what if’ conditions. This enables you to test in advance whether proposed changes, or their manner of implementation, will or will not deliver the anticipated benefits.
Through carrying out dynamic program simulation on a range of complex assets, we have shared the following lessons with management:
- net benefits of individual changes to production vary significantly with the degree of disruption they cause
- benefits of design/process changes depend on other program conditions and changes
- cumulative program change can exceed capacity to effectively mitigate associated disruption.
Achieving cost reduction through dynamic program simulation
Our work with the US Navy provides a good illustration of this approach. The Navy planned to increase production of their VIRGINIA Class nuclear attack submarine from one to two boats per year, on the proviso that costs could be reduced by $400 million (about 20%) for a potential $12.4 billion in total savings. Achieving cost reduction on this mature program had to occur without disrupting the excellent performance to date. We worked collaboratively with the Program Office and two shipbuilders, using dynamic program simulation to evaluate net labor hour and schedule impacts of design, production process, workforce and other changes. Our analysis provided a clear, realistic view of likely cost reduction and helped stakeholders agree an effective path forward.