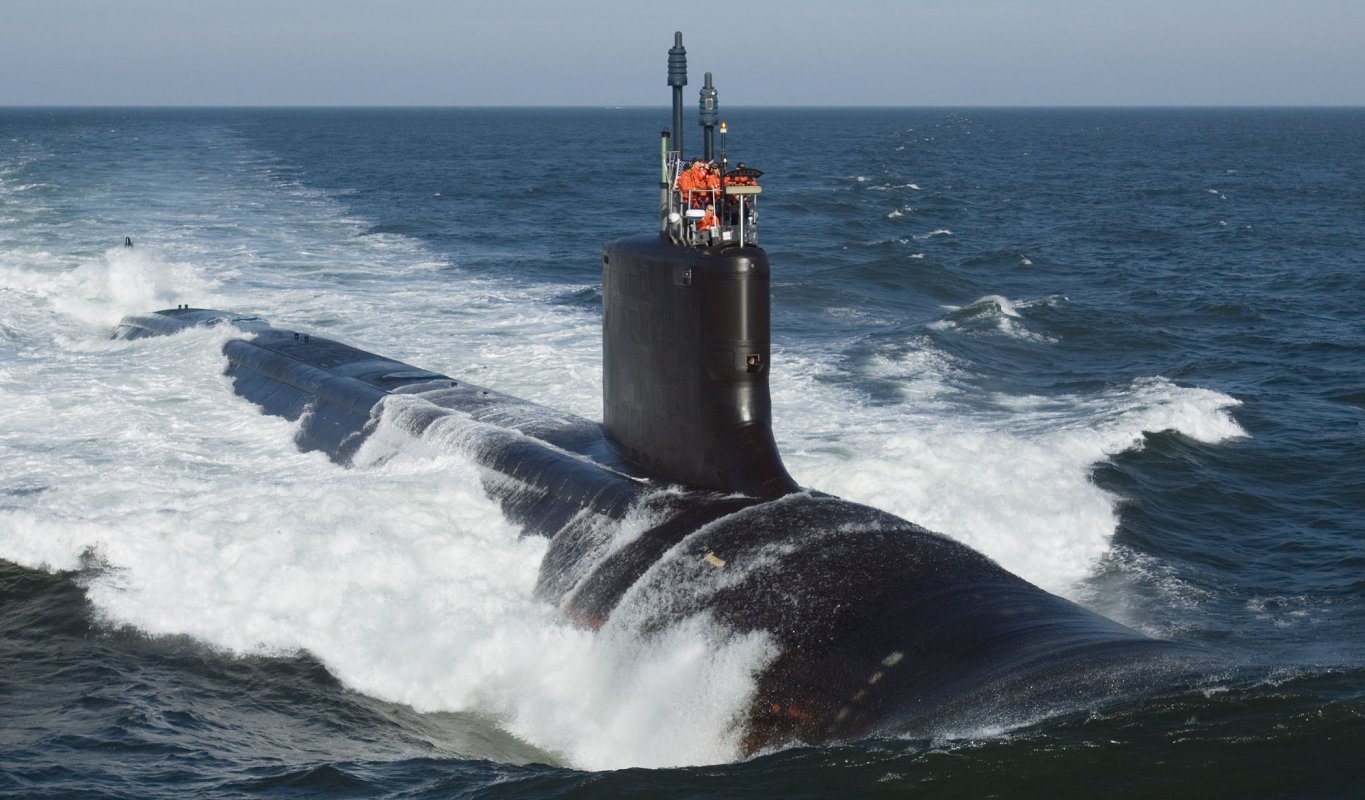
This article first appeared in Naval Engineers Journal on 9/1/11. The article was awarded the 2011 Jimmie Hamilton Award by The American Society of Naval Engineers for best original paper published in the Naval Engineers Journal.
“The authors explained the fundamental aspects involved in both clearly written and well-presented graphical forms that made this paper stand out from other papers. The authors have demonstrated superior knowledge of the subject matter, and explained it so that a wide audience can benefit from the results of this study. The authors are highly deserving of the Society’s 2011 Jimmie Hamilton Award.”
By Christy I. Goff, Charles L. McNamara, Joseph M. Bradley, Christopher S. Trost, William J. Dalton, & Michael E. Jabaley, Jr.
To get the most value from high-value assets such as ships, power-plants and oil-rigs, you need to find the right balance between maintenance, modernization and operational activity so as to extend service life, enhance performance and minimize ‘down-time’ over the asset lifecycle.
In many organizations, however, undue pressure to maximize immediate return from high-value assets by pushing their performance to the limit frequently creates a stove-pipe mentality that does not factor in the other activities and only focuses on profit. Such a mentality misses the long-term implications of neglecting asset maintenance, for example, or it focuses activity too much on one area. As a result, lifecycle performance is compromised – as are long-term financial returns.
By measuring the trade-off between performance, down-time and risk through a ‘dynamic simulation’ model, you can balance maintenance activity, operational policy and performance constraints to get the most out of your asset, across its entire lifecycle.
Keeping track of the maintenance backlog
A dynamic simulation analyses operations and maintenance activity and performance constraints to provide a clear view of an asset’s backlog. The critical backlog is the difference between a level of maintenance that would extend an asset forever, and the level of maintenance that is actually practical. It shows the asset’s condition, its risk of failure and the maintenance required for optimum performance. Over time, the backlog grows through ‘insidious decline,’ the increase in the wear of a system as components wear out, which affects the rate of wear of other components. Ordinarily, without a dynamic simulation, it is difficult to manage because system failures only become apparent after a time lag and its long-term effects on performance are not linear.
Managing trade-offs with dynamic simulation
Dynamic simulation shows you the impact of different options across organizational boundaries, such as operations and maintenance, which can otherwise be constrained by isolated and stove-pipe thinking. It allows you to focus on current revenue in the light of the asset’s lifecycle and targeted total returns. You can thereby make trade-offs between cost and risk to performance, which is necessary to meet objectives across the asset lifecycle. Achieving options across organizational boundaries results in higher returns by helping people understand the impacts that jeopardize future returns from the asset.
Creating savings of $2 billion through better lifecycle planning
A strong example of dynamic simulation in action is the US Navy. They are in a position where they don’t have enough submarines to support their stated fleet requirements. As defense budgets are under extreme pressure, and submarines cost billions of dollars, buying more is not an option. Using dynamic simulation to coordinate policy, design and maintenance changes, we identified how submarines can add an additional two-year deployment cycle (6% increase in operational time) within their fixed 33-year lifetime. The additional deployment time provides the capability of an additional submarine – an asset worth at least $2 billion – at negligible cost.