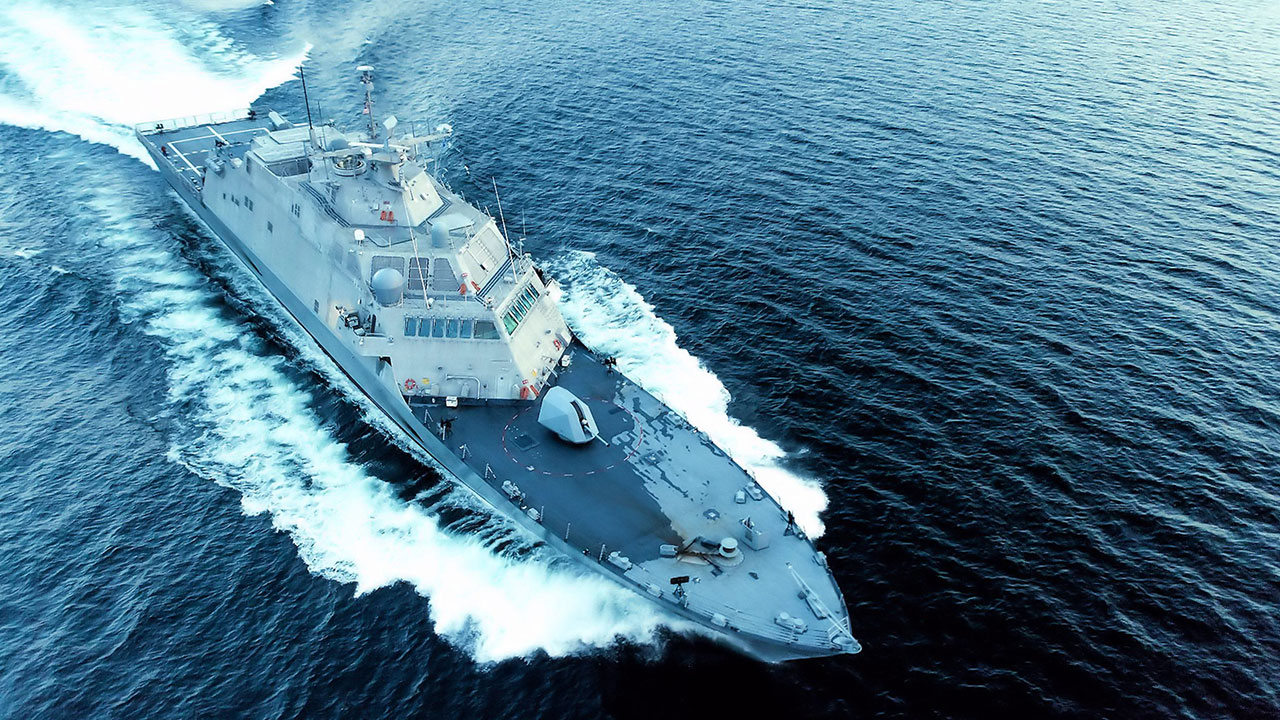
This article first appeared in Naval Engineers Journal on 3/1/18.
By CAPT Chris Mercer USN, David Barksdale, Christopher S. Trost & Donna D. Mayo
The US Department of Defense specifies an approach to determine an acquisition program’s “should-cost” as a separate input from the “will-cost” or traditional cost evaluation for developing a negotiating strategy. Will-cost is based on analysis of historical costs and trends to determine a price. Should-cost does not assume that historical costs reflect efficient and economical operation but instead evaluates the “efficiency of the contractor’s work force, methods, materials, facilities, operating systems, and management.” (Federal Acquisition Regulations 15.810) Getting program labor costs as low as possible or towards a should-cost requires an inherent understanding of the productivity that can be achieved given the conditions under which the program will be executed. Understanding these conditions is also crucial to identify which actions should be taken and at what time to influence labor productivity positively and thus improve overall program performance. Determining the should-cost for labor therefore necessitates understanding how the workforce, methods, facilities, operating systems and management actions interact within the overarching facility dynamics and over the course of the program to drive productivity and quality and thus overall performance.
Developing should-cost positions was a primary focus of a large, complex shipbuilding program that came on the heels of a preceding project that experienced unacceptable cost and schedule delays. The program had to incorporate and assess the impact of lead ship performance issues and lessons learned, shipyard-wide safety, quality and performance improvements, planned design changes, real budgetary reductions, and government acquisition improvements including should-cost measurement techniques into the follow ship.
Within this construct, the program team had to identify opportunities to improve outcomes for government and industry on the follow ships. The program office segregated costs into 3 roughly equal areas for should-cost analysis: labor, material and overhead. Initiatives were undertaken on both material and overhead focused on reducing costs from the preexisting baseline. Developing a labor should-cost proved to be more complex and required assessing and forecasting the labor hours involved instead of the cost of labor. The ability to quantify labor productivity and readily identify actionable initiatives to improve performance was needed. A system dynamics based program simulation proved to be an excellent complementary tool to usual and customary metrics and together, provided the requisite understanding and quantitative analysis of labor productivity needed to develop should-cost initiatives and should-cost targets.
The program simulation was first developed using Navy available data and information and was subsequently reviewed and updated with shipyard input to guide both parties in improving performance. The model development process also provided significant side benefits to the program teams by advancing their understanding of the drivers of productivity and quality and how different types of actions influence labor cost and schedule performance throughout design and production. The simulation was used to assess the impact of design changes including how and when they were implemented, evaluate and adjust policies, plans and schedules, monitor ongoing performance and forecast formal program office estimates at completion (EAC). Examples of how the simulation was used to evaluate the initial Integrated Master Schedule (IMS) and analyze contract incentives with a focus on moving towards labor should-cost are described.